Phoenix 3D Printing is a fabrication method used to create three-dimensional objects. The printing process involves building layers of materials until the object is complete.
The technology is used in many industries. Some companies use it to make tools, jigs, and fixtures, while others build end-use products. The benefits of 3D Printing are numerous:
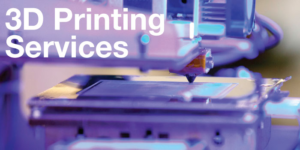
With 3D printing, engineers can quickly transform digital concepts into physical prototypes for testing and feedback. This allows for a faster, more efficient product development cycle and reduces the time needed to get to market.
The rapid prototyping process begins with a CAD model of the product, which is then converted into a STL file (STL files are a cross-sectional representation of a 3D design that the printer can build upon layer by layer). Once the STL file has been sliced, the 3D printer builds up layers of material until the entire prototype is complete. The resulting prototype may require post-processing to remove support structures, smooth surfaces and add paint or other finishes.
Once the initial prototype is printed, it is shared with users to collect feedback and evaluate its usability and functionality. When collecting bona fide user feedback, it is important to make sure that the users aren’t aware that they are interacting with a prototype so that they provide genuine reactions and honest insights.
When the initial feedback is analyzed and synthesized, the team can use it to refine the design of the prototype and create a new version for further testing. This process is repeated until the design meets a specified cut-off point, which might be a certain date, a number of iterations or a clear indication that the design is ready to go into production.
The ability to quickly produce prototypes also helps identify and address design flaws early on in the process, which can save significant time and money by preventing the need to spend resources on a product that won’t meet market demands. In addition, the ability to quickly convert a digital design into a physical model enables collaboration with industrial designers and other partners to validate aesthetics and ergonomics, as well as test the performance of the product’s materials and mechanics. This ensures that the design is both functional and aesthetically appealing, and that the final product will be successful once it goes into production. The process also encourages user input throughout the design and testing phases, which can help avoid unforeseen issues once the product is in production.
Better Quality Prototypes
3D printing offers a high level of design flexibility and allows companies to produce prototypes in-house. This means that manufacturers and product designers do not have to rely on the time-consuming process of waiting for a shipment from a remote location. With in-house 3D printing, products can be designed, fabricated, tested, and refined within days. This allows for faster development cycles and can give businesses a competitive edge.
The first step is to create a digital model using computer-aided design (CAD) software. This can be a simple sketch or a fully detailed 3D representation of the final product. The model can then be converted into an STL file format. This file contains a set of instructions that the 3D printer will use to create the physical object.
Once the STL file has been generated, a slicer is used to split the model into thin layers. Each layer is then deposited onto the build plate one at a time, and the 3D printer creates the object based on these instructions. Depending on the type of 3D printer, the layers may be fused together or separated by an air gap to create a more solid structure.
When the layering is complete, a finishing technique can be used to smooth out the surface of the product. For example, a coat of paint can be applied to the finished print or the part can be sanded down to expose the metal. Alternatively, an adhesive can be used to adhere the parts together.
One of the most important advantages of 3D printing is that it can be used to make a wide range of materials, including plastics and metals. This can help to increase the durability of the finished product and allow for greater design flexibility. Additionally, the ability to print a variety of materials can be beneficial for businesses looking to develop prototypes with specific properties or aesthetics.
Although 3D printing is becoming increasingly popular, it does have some limitations that must be considered. For example, a large part might not fit on a 3D printer’s build plate and may require splitting into smaller components for production. Additionally, the quality of prints can vary based on printer limitations and the design of the finished product.
Lower Costs
Compared to traditional manufacturing methods, 3D printing has lower overheads and costs. This is due to the fact that most of the labour involved in producing a 3D printed part comes from preparing software and finishing parts after printing, rather than from making a mould or machining. Additionally, material costs are relatively low with most models only costing a few dollars to produce (depending on the printer and materials used).
Another way that 3D printing helps reduce costs is by allowing for rapid prototyping. Since a prototype can be made in a short amount of time, it is possible to experiment with different designs and ideas more often. This allows for a quicker and more effective product development cycle, which in turn can lead to improved quality products.
Furthermore, as 3D printing is based on digital technologies, changing a prototype can be done at any stage of the process without incurring additional costs. This is because the product design engineers work digitally and only need to change the CAD data to produce a new iteration of the prototype, rather than having to manufacture a new mould or machine a new component from scratch.
As a result, the iterative nature of 3D printing can help to eliminate costly mistakes in production and improve overall product quality, which can have significant financial benefits for companies. Additionally, as the cost of printing continues to decrease, it is becoming more affordable to produce components or finished products locally, which can save on shipping costs and reduce production lead times.
Lastly, the flexibility of 3D printing can also cut costs by allowing companies to produce parts on demand. This can be done either through the purchase of a 3D printer or by outsourcing the production of parts to a service provider like Roboze 3D Parts.
The ability to print parts on demand can also help to reduce inventory costs, as companies don’t need to keep large stocks of parts or products in storage. This can be especially useful in industries that are experiencing frequent changes in technology or design, as it is much easier to create a new model or prototype with 3D printing than it would be with conventional manufacturing techniques.
Faster Production
Using 3D printing to create prototypes provides companies with a low-risk way of testing their product’s efficiency, ramping up production or making repairs without having to invest in expensive models or proprietary tools. This can result in shortened delays and quicker product time to market, and it can help manufacturers save money by eliminating the cost of manufacturing and assembly.
3D printing is also a great teaching tool for students in science, technology, engineering and math subjects (STEM). Students learn to design and model, problem-solve and pay attention to detail, all skills that are important when working with 3D printers. They also learn how to print items that are functional and resemble the actual item they are trying to recreate, which can help them understand the mechanics of how the object works.
Many 3D printing methods use layer upon layer of raw materials to build the item, similar to how an ink printer works. The materials are then fused together to create the finished item. This process can take a while, depending on the type of printer and the size of the object being printed. The surface finish of the item can also affect how long it takes to complete, and items with fine details may require additional post-production finishing processes to get a smooth surface.
There are several ways to speed up the printing process, including increasing the print speed in the slicer settings. However, this should be done carefully to avoid compromising printing quality or precision. Another option is to increase the layer height. This will reduce the number of layers needed to complete the print, and subsequently, the printing time. It is important to test the new layer height on a test piece before applying it to production prints.
Finally, removing or optimizing support structures and rafts can also significantly reduce the printing time. Additionally, increasing the infill pattern and density can further decrease the printing time. This should be tested on a sample print to ensure that the infill does not impact printing precision.